3D Laser Metal Printing
Design and development of Direct Metal Deposition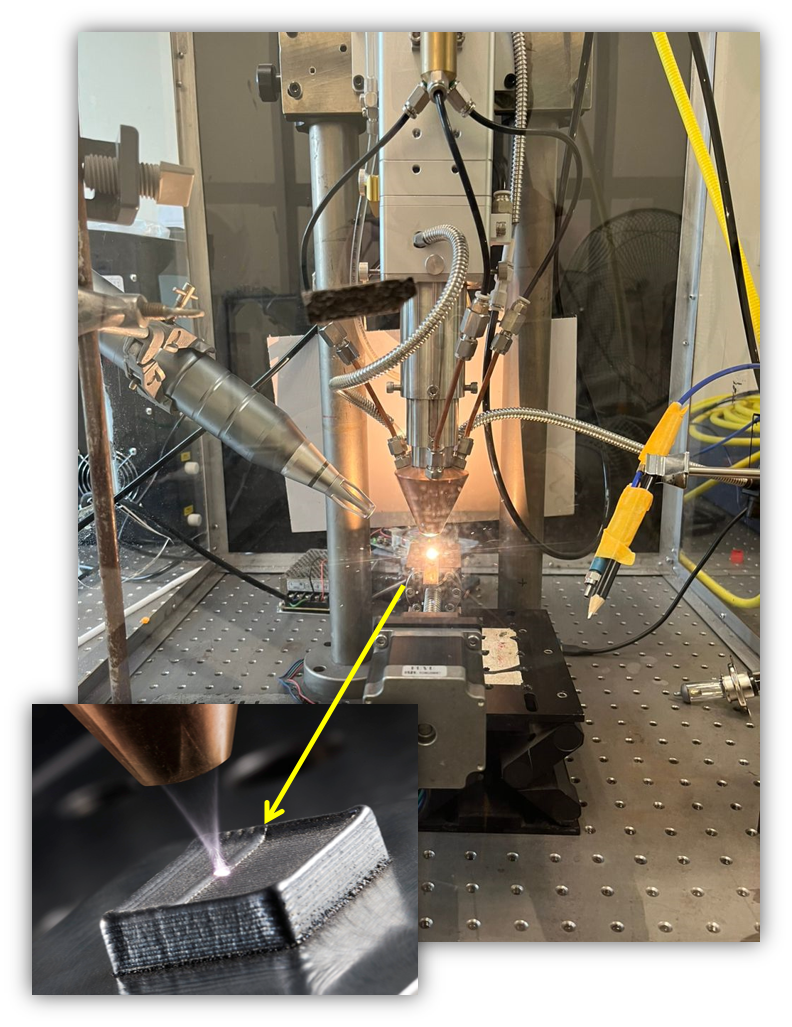
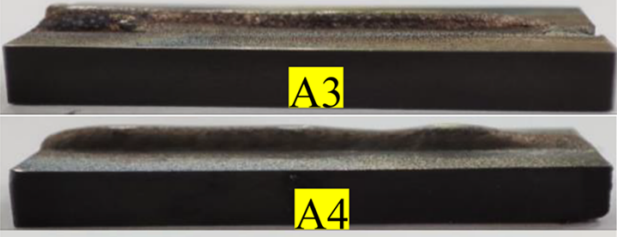
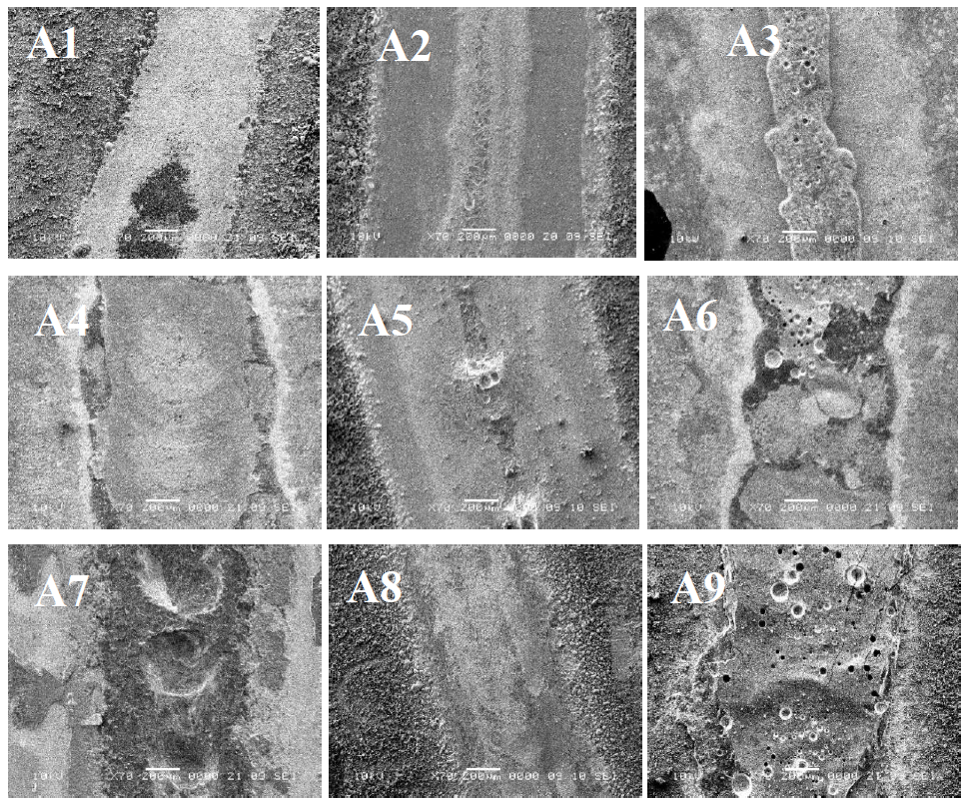
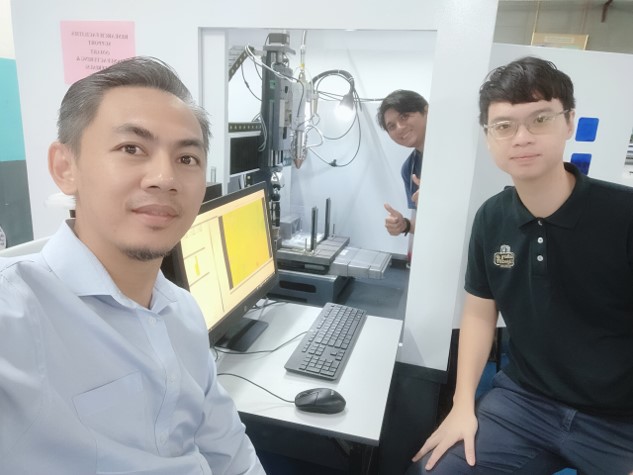
3D metal printing has revolutionized manufacturing by enabling the creation of complex and customized metal components with high precision. One of the advanced methods utilized in this domain is the Direct Metal Deposition (DMD) technique, which has been developed and refined at Universiti Teknologi Malaysia (UTM).
The DMD process involves the precise deposition of metal powders or wires directly onto a substrate using a laser as the heat source. This method allows the material to melt and fuse layer by layer, building the desired component with exceptional mechanical properties and metallurgical bonding. At UTM, the DMD system incorporates state-of-the-art laser technology and a controlled material delivery system, ensuring optimal process stability and high-quality output.
Our advancements in DMD technology focus on enhancing deposition accuracy, improving the microstructure of the printed metal, and minimizing residual stresses. This has allowed for the production of durable and lightweight components suitable for aerospace, automotive, and biomedical industries. Additionally, the versatility of this method enables the repair of high-value components and the addition of functional features to existing parts.
The development of DMD at UTM underscores the commitment to innovation in advanced manufacturing techniques, contributing to the global push for sustainable and efficient production technologies.