Posted on Dec 14, 2023 · (Edit)
This course integrates both the manual components and the cognitive aspects of work. Motion and time study, human factors and ergonomics to produce precise work sequence and to form standard inventory, including units in machines required to keep the manufacturing/service process operating smoothly and efficiently. The importance of ergonomics and work design as part of methods engineering is emphasized not only to increase productivity, but also to improve worker health and safety, and thus, company bottom-line costs. Topics covered: Work standardization, work measurement and standardization processes; participant involvement. Waste identification, Method Analysis. Work standardization Techniques: Time Study, calculating the standard time for manufacturing tasks. Productivity analysis. Work Methods Improvement. Work sampling and labour reporting issues. Product improvement ergonomics, incentive systems. Work Management, case studies including ones showing applications with the service
industry.
Introduce your self
Name, Education, Working Experience and background, Research interest, Hobby
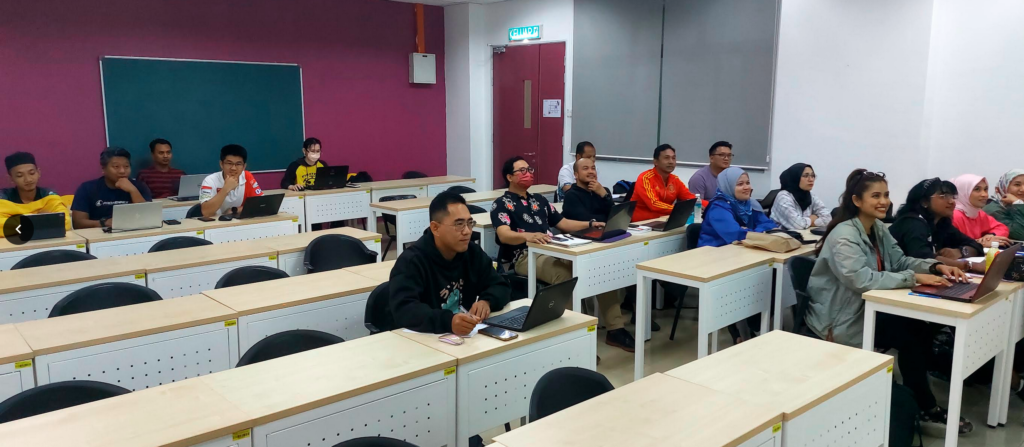
Work Standardization
Definition:
Work standardization is a lean manufacturing and management concept that involves creating and documenting the best, most efficient way to complete a task. It aims to reduce variability and improve quality, safety, and efficiency.
Key elements:
- Takt time: The rate at which work needs to be done to meet customer demand.
- Work sequence: The specific steps involved in completing a task, in the most efficient order.
- Standard inventory: The amount of materials needed to keep the process running smoothly.
- Standard operating procedures (SOPs): Written documents that detail the work sequence and other important information.
- Visual controls: Andon cords, kanbans, and other visual aids that help to identify problems and track progress.
Benefits:
- Improved quality and consistency
- Reduced waste
- Increased efficiency and productivity
- Improved safety
- Better employee training and development
- More consistent customer experience
Implementation steps:
- Identify the process to be standardized.
- Analyze the current process and identify variations.
- Develop the standard work sequence.
- Document the standard work sequence in SOPs.
- Train employees on the standard work sequence.
- Monitor and audit adherence to the standard work sequence.
- Continuously improve the standard work sequence.
Challenges:
- Resistance to change from employees and management
- Difficulty identifying the best way to do the work
- Lack of communication and training
- Difficulty measuring the impact of work standardization
Examples of standardized work:
- Assembly line processes
- Service processes, such as order processing and customer service
- Administrative tasks, such as data entry and document review
Additional resources:
- TWI Institute: https://www.twi-institute.com/standard-work-certification/
- Six Sigma Study Guide: https://sixsigmastudyguide.com/six-sigma-study-guides/
- SweetProcess: https://tulip.co/glossary/what-is-standardized-work-and-how-to-apply-it/
CASE STUDY 1
- You are a team leader responsible for a production line. You notice that there is a lot of variation in the quality of the products being produced. What steps could you take to implement work standardization and improve quality?
- You are a customer service representative. You often receive complaints from customers about inconsistent service experiences. How could work standardization help to improve customer satisfaction?
CASE STUDY 2
- Discuss the advantages and disadvantages of work standardization.
- How can work standardization be used to promote continuous improvement?
- Describe some of the challenges of implementing work standardization in an organization.
TEST
- Multiple Choice
- What is the primary benefit of work standardization?
- (a) Increased confusion and guesswork
- (b) Reduced variability and improved quality
- (c) Increased individual creativity
- (d) None of the above
- What is one of the key elements of standardized work?
- (a) Individual preferences and interpretations
- (b) Documented best practices and procedures
- (c) Encouragement of experimentation and deviation
- (d) Lack of specific guidelines and expectations
- What is the role of training in work standardization?
- (a) To make employees feel comfortable ignoring the standards
- (b) To demonstrate how to disregard established procedures
- (c) To ensure everyone understands and can follow the standards
- (d) To show employees how to personalize the standards
2. True or False:
- Work standardization is only necessary for complex tasks.
- Standardized work can be used for both production and service processes.
- Continuous improvement is not part of work standardization.
- The goal of work standardization is to eliminate all human interaction.
3. Fill-in-the-Blank
- Standardized work is a documented set of _______ that describe the best known _______ for completing a task.
- One of the benefits of work standardization is improved _______ and _______
- Standardized work can be used to identify _______ and opportunities for _______.
PMA-WS_18-Dec-2021_Work-Standardization-2-1Download
POST MODULE ASSESSMENT (PMA)
Objective: To enhance students’ appreciation on the importance of understanding Work Standard issues for the development of organisations/industry
Write a report on Work Standard based on your experience at workplace:
Chapter 1 – Introduction
Introduction of the company
Chapter 2 – Review of Ergonomics
Pillars of Ergonomics – identify and describe the type of physical ergonomics adopted by your division/department/company
- What are the advantages and drawbacks?
Chapter 3 – 5S in your workplace
Good, Bad and Ugly
Chapter 4 – Kanban and Kaizen
Overview of Kanban and Kaizen
Chapter 5 Discussion and Conclusion
References
Prepare a PMA in 15-20 pages and send the report to Razak Faculty of Technology and Informatics, Level 7 Menara Razak, UTM Kuala Lumpur before 18 Jan 2024.
Submit Case Study 1 (20%) HERE before 6 pm on Dec 18, 2023
Submit Case Study 2 (20%) HERE before 6 pm on Dec 18, 2023
Submit Test 1 (20%) HERE before 6 pm on Dec 18, 2023
Submit PMA (40%) HERE before 18 January 2024