This course integrates both the manual components and the cognitive aspects of work. Motion and time study, human factors and ergonomics to produce precise work sequence and to form standard inventory, including units in machines required to keep the manufacturing/service process operating smoothly and efficiently. The importance of ergonomics and work design as part of methods engineering is emphasized not only to increase productivity, but also to improve worker health and safety, and thus, company bottom-line costs. Topics covered: Work standardization, work measurement and standardization processes; participant involvement. Waste identification, Method Analysis. Work standardization Techniques: Time Study, calculating the standard time for manufacturing tasks. Productivity analysis. Work Methods Improvement. Work sampling and labour reporting issues. Product improvement ergonomics, incentive systems. Work Management, case studies including ones showing applications with the service
industry.
Introduce your self
Name, Education, Working Experience and background, Research interest, Hobby
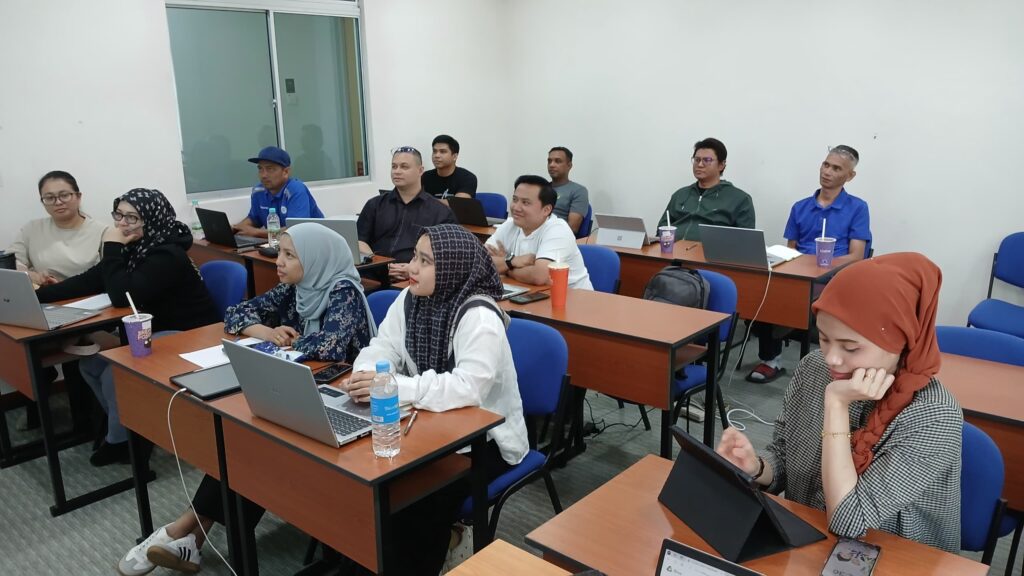
17 August 2024
From left to right: Nabilah, Shazlin, Linda, Ain, Atiqqah
Second row form left to right: Amir, Airie, ‘Aroff
Third row from left to right: Aemierul, Mogaan, Arif and Badrul
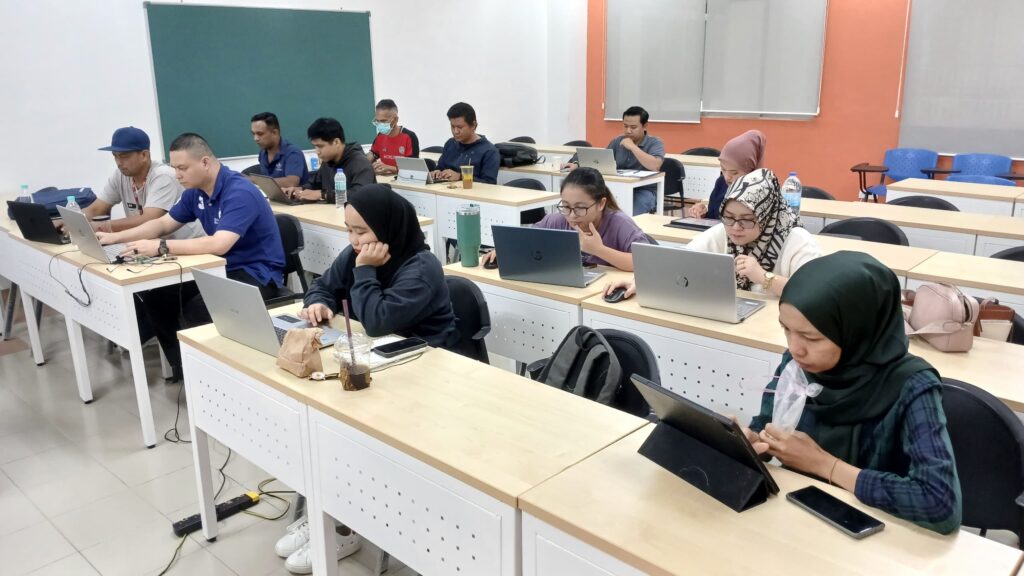
18 August 2024
1st row: Amir, Airie, Ain, Linda
2nd row: Mogaan, Aemierul, Nabilah, Shazlin
3rd row: Badrul, Arif, Atiqqah
4th row: ‘Aroff
Case Study 1 (20%)
Group presentation
- You are a team leader responsible for a production line. You notice that there is a lot of variation in the quality of the products being produced. What steps could you take to implement work standardization and improve quality?
- You are a customer service representative. You often receive complaints from customers about inconsistent service experiences. How could work standardization help to improve customer satisfaction?
Case Study 2 (20%)
- Discuss the advantages and disadvantages of work standardization.
- How can work standardization be used to promote continuous improvement?
- Describe some of the challenges of implementing work standardization in an organization.
Test 1 (20%)
Question 1: Work Standardization Techniques (25 marks)
Explain the process of conducting a time study in a manufacturing environment. Describe each step in detail, and discuss how you would calculate the standard time for a specific task. Assume that the task involves assembling a small mechanical part. Include factors such as allowances for rest and fatigue.
Question 2: Ergonomics and Work Design (20 marks)
Ergonomics plays a critical role in the design of workstations to ensure worker safety and efficiency. Discuss the ergonomic principles that should be considered when designing a workstation for an assembly line worker. Provide examples of how poor ergonomic design can lead to reduced productivity and increased health risks.
Question 3: Method Analysis and Waste Identification (20 marks)
You have been tasked with improving the efficiency of a service process in a retail environment. Outline the steps you would take to conduct a method analysis. Identify potential areas of waste in the process, and suggest improvements that could be implemented to enhance efficiency and reduce waste.
Question 4: Work Sampling and Labour Reporting (15 marks)
Describe the work sampling technique and explain how it can be used to measure the performance of workers in a service industry, such as a call center. What are the advantages and limitations of using work sampling compared to continuous observation?
Question 5: Case Study Analysis (20 marks)
Consider a case where a manufacturing company implemented an incentive system to boost productivity. The system rewarded workers based on the number of units produced above a certain threshold. After a few months, the company observed an increase in defects and a decline in product quality. Analyze the situation, identifying the root causes of the issues. Suggest how the incentive system could be modified to balance productivity and quality.
FRSI 2403: WORK STANDARDIZATION (40%)
POST MODULE ASSESSMENT (PMA)
Objective: To enhance students’ appreciation on the importance of understanding Work Standard issues for the development of organisations/industry
Write a report on Work Standard based on your experience at workplace:
Chapter 1 – Introduction
Introduction of the company-Background of Industry/Organization
- Company Profile
- Organization Structure
- Information of the industry/organization where the Project is conducted
- Work flowchart of the industry/organization
Chapter 2 – Review of Ergonomics
Pillars of Ergonomics – identify and describe the type of physical ergonomics adopted by your division/department/company
- What are the advantages and drawbacks?
Chapter 3 – 5S in your workplace
Good, Bad and Ugly
Chapter 4 – Kanban and Kaizen
Overview of Kanban and Kaizen
Chapter 5 Discussion and Conclusion
References
Note: Prepare a PMA in 15-30 pages and please email your PMA to shamsuls.kl@utm.my before 19 Sept 2024.
Many thanks
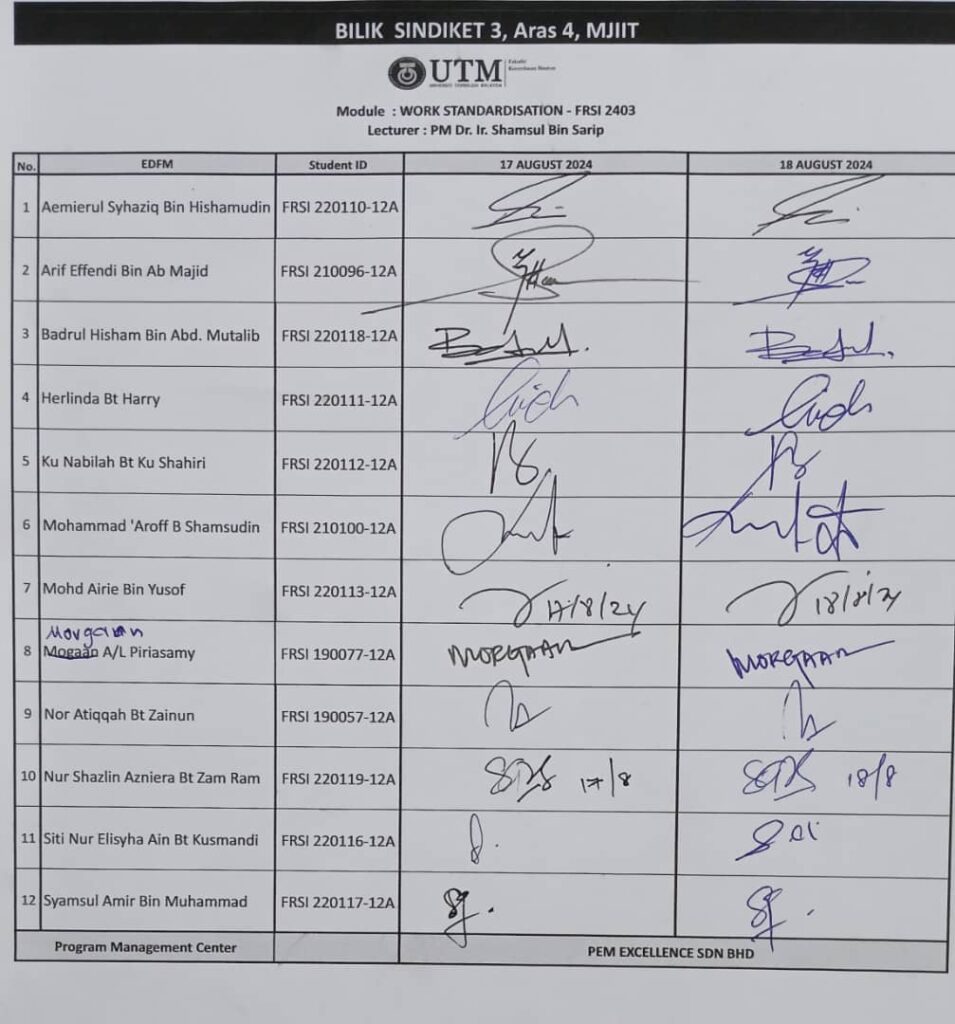